We’ve used their smallest planers right up to their largest planers, depending on the nature of the project and every time have been delighted with the results of the works. They’re a fantastic company to work with.
Setting the standard
For sustainable road planing in the UK
Delivering an enhanced road planing service, with a vision to achieve carbon neutrality across the most demanding and technically challenging projects.
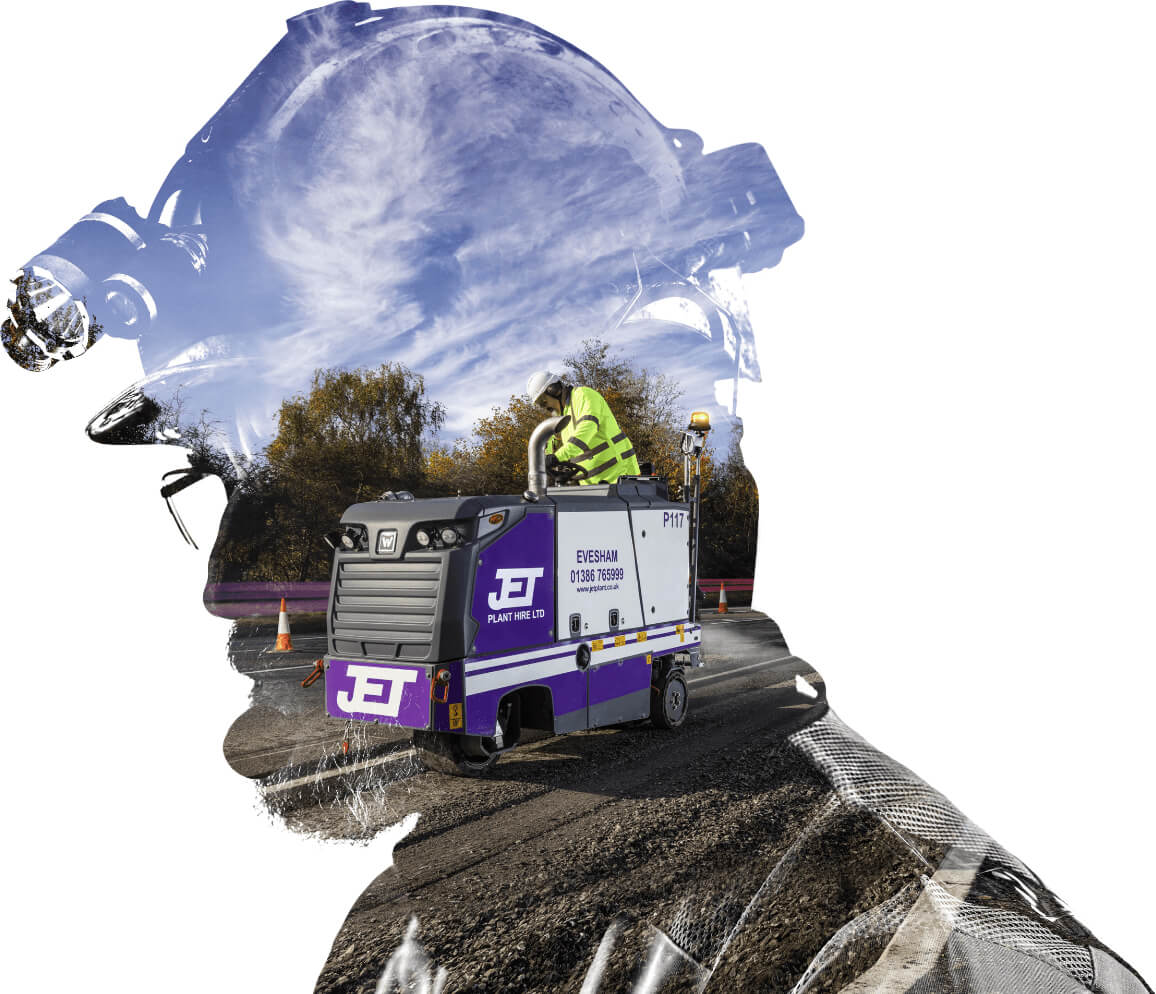
Introducing our Groundbreaking new 1m planer
Experts in process and programme management
We at Jet Plant are powered by an industry defining combination of exceptional people and our continual innovation and development. With job quality and carbon net zero operations as our driving force, we invest in the finest state of the art equipment, working ethos, project capability and availability of the planing service and consultancy support you need when you need it. Our team deliver scalable solutions for all types of customers.
How we set the standards by which others are judged
Sustainable Innovation
Jet Plant offer high performance, state-of-the-art planers operated by industry experts will optimise your solution to mirror your carbon commitments. Driven by informatics, our world-leading equipment and management technologies are capable of delivering tangible reductions in emissions across all projects.
Business Ethics
Fully accredited, accountable and sustainable, our service promise is to go above and beyond to enhance the reputation of our customers. Integrity drives everything we do which is why we only employ sector-leading professionals who are committed to delivering complete customer satisfaction.
Process Rigour
Our highly experienced teams work side-by-side with your organisation, delivering an enhanced service, tailored to your specific requirements – meaning you don’t have to worry about the planing. Jet Plant are committed to effective and efficient project delivery.
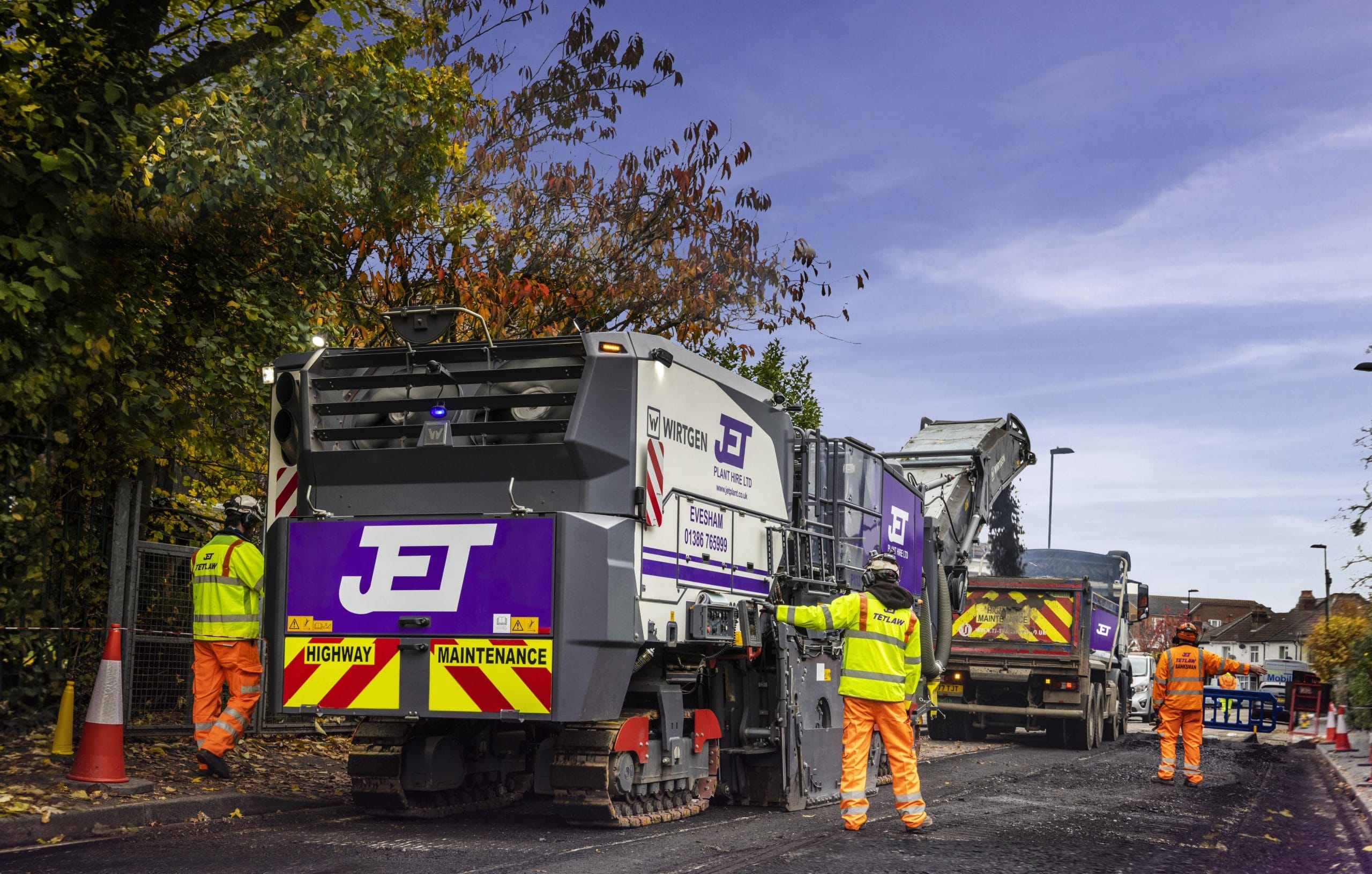
REGIONAL EXPERTISE, NATIONAL CAPABILITIES
With a vast fleet of state-of-the-art road planers and a strategic network of depots, Jet Plant is your trusted partner for road planing projects nationwide. Our expert team, cutting-edge equipment, and unwavering commitment to quality ensure that we can efficiently and effectively serve projects of any scale, from small local road repairs to major highway expansions.
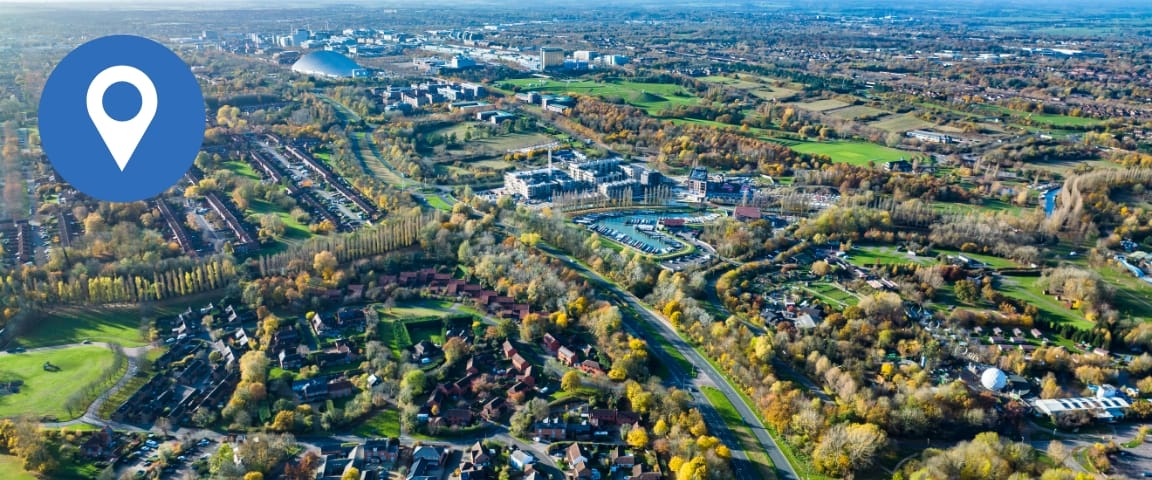
Central
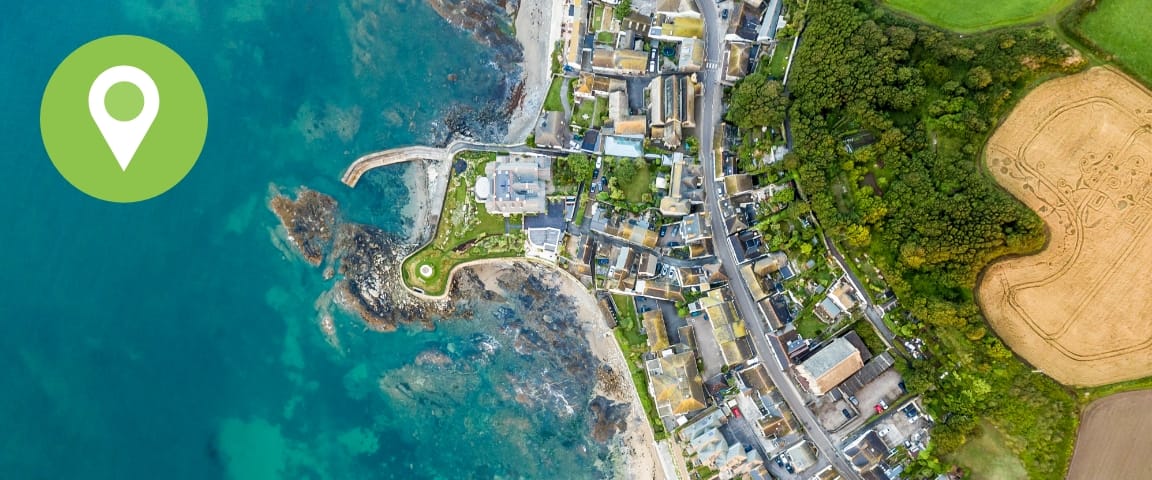
South
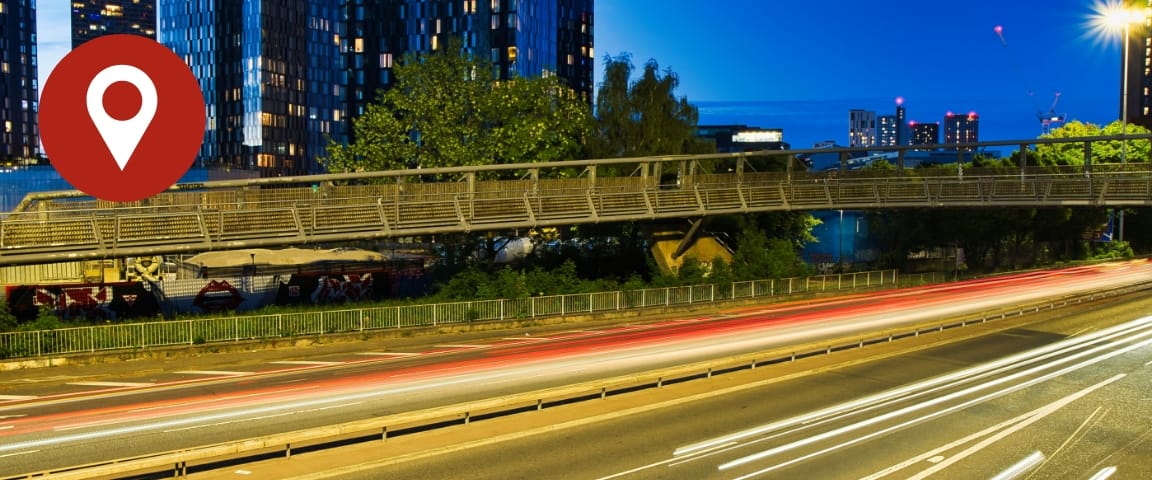
North
Testimonials
It can sometimes be the case that we approach them with a project and ask for their opinion on what planing and sweeping equipment we need and they always come up with a solution that delivers.
Contracts Manager
I have used Jet Plant for 21 years now since my very first day – all these years later and I have no intention of going elsewhere. Time after time they deliver, all while providing outstanding customer service.
Contracts Manager
As our projects are so varied so are our requirements, yet every single time Jet Plant Hire come through, even with minimal notice, providing an excellent service.
Contracts Director
We find that they are always happy to accommodate whatever our requirements may be, while making the whole process seamless from start to finish.
Commercial Manager
When it comes to Jet Plant Hire, nothing is too much. I have worked with them for over 16 years now and their reputation remains the same; hands on, available and reliable.
Area Manager
Jet Plant Hire has been one of our core planing equipment providers for over a decade now and, no matter the size and scale of the project, they deliver every single time.
Contracts Manager
I cannot fault Jet Plant Hire, they are excellent and an invaluable partner to us and we’re very grateful for their continued efforts.
Contracts Manager
Excellent service, highly efficient and the highest of quality – all words I associate with Jet Plant Hire. Our experience from day one, back in 2012, has been nothing but fantastic.
Contracts Director
Jet Plant are fantastic – a reliable, easy to deal with, friendly partner that consistently provides us with outstanding customer service. They are without doubt our supplier of choice for planing equipment.